
Fabricated Orifice & Transition Rings for Steam Boiler Applications
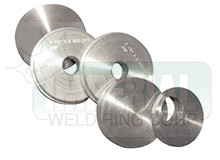
Orifice rings are commonly used in forced circulation boilers to maintain proportional flow or produce a throttled/choked flow at the ring's location within the line. By controlling flow rate, orifice rings help to prevent steam blanketing and tube overheating, which can cause damage to boiler systems. Imperial's orifice rings can also serve as diameter transition rings, commonly referred to as "step rings" or "step-down rings," for welding pipe or tubes with different inside diameters. The step-down ring has a tapered transition at its center, which serves as the weld root opening. This not only simplifies fit-up, but also eliminates an abrupt shoulder at the joint.
At Imperial Weld Ring, we are regularly asked by our utility, power generation, energy, and steam turbine customers to fabricate orificed backing rings for steam boiler applications. We manufactured these orifice rings for joints with similar and dissimilar walls, and often supplied them for use with flat or taper-bored ID prep. After we developed custom work holding fixtures, we employed CNC turning and milling to precision machine the rings, and then polished all surfaces to 63Ra max finish, followed by a coating of weldable primer. We also conducted go / no-go gauging inspections, fully maintained material heat/lot traceability, and confirmed precision machined tolerances of ±0.002" with custom gages and calibrated measuring equipment.
We were comfortable producing anywhere between 1 and 20,000 of the parts. We also prototype the rings and provided maintenance contracts and rush or emergency services for our customers. These rings are fabricated to ASME Boiler & Pressure Vessel Code, Section III, Division I, Subsection NCA-3800 standards, as well as customer engineered specifications. We made 20,000 of the rings in only one to two weeks and delivered them to customers worldwide.
At Imperial Weld Ring, we used this project to demonstrate ourselves as an industry leader in the fabrication of boiler components and pressure parts. To discover more about our skills, contact us directly.
Orifice & Transition Rings Project Highlights
- Project Name
- Orifice & Transition Rings
- Project Description
- Solid Ring / Disc with a drilled hole (centered or offset) installed within a pipeline system to control flow rate. Orifice rings are commonly used in forced circulation boilers to maintain proportional flow or produce a throttled / choked flow at the ring's location within the line. By controlling flowrate, the orifice rings helps to prevent steam blanketing and tube overheat which can cause damage to boiler systems.
- Capabilities Applied/Processes
- Primary:
CNC Turning & Milling
Drilling
Tubular Swaging
Precision Machining
Pipe Beveling
Secondary:
Saw Cutting
Deburring
Polishing
Weldable Primer Coating
Gauging and Inspection
- Equipment Used to Manufacture Part
- CNC Turning Lathes
Manual Engineer / Turret Lathes
Bridgeport Mills
Drill Presses
Vertical & Horizontal Band Saws
Custom Gages
Custom Workholding Fixtures
Calibrated Measuring and Inspecting Equipment
- Overall Part Dimensions
- Part dimensions vary per customer requirements
- Tightest Tolerances
- ± 0.002"
- Material Used
- Material supplied to match chemical and physical characteristics of parent tube, typically Chrome Moly, Stainless, & Nickel Alloys
Materials used are as follows:- ASME SA-178 GR. A
- ASME SA-182 F22 CL.3
- ASME SA-182 F91
- Material Finish
- 63Ra max all surfaces
- Additional Facts
- Transition rings, also commonly referred to as "step rings" or step-down rings," are for welding pipe or tubes with different inside diameters. The ring has a tapered transition at its center which serves as the weld root opening. This not only simplifies fit-up but also eliminates an abrupt shoulder at the joint.
- In Process Testing/Inspection Performed
- Go / No-Go Gauging
Material Heat / Lot Traceability Fully Maintained
- Industry for Use
- OEMs
Utilities
Power Generation
Coal, Oil, Natural Gas, and Nuclear Energy
Alternative Fuels
Cogeneration Facilities
Boilers
Steam Turbines
- Volume
- 20,000 Annually
Order Size: Any Okay, from 1 part to 20,000 parts
Prototyping
Maintenance Contracts
Rush Parts for Emergencies / Outages
- Delivery/Turnaround Time
- 1 - 2 Weeks or as Required
- Delivery Location
- Worldwide
- Standards Met
- ASME Boiler & Pressure Vessel Code, Section III, Division I, Subsection NCA-3800
Customer Engineering Specifications
Precision Machining Tolerances